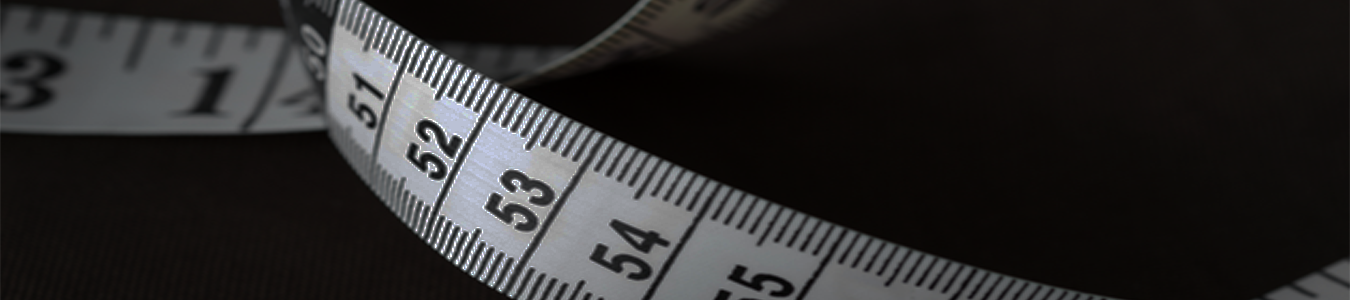
Process
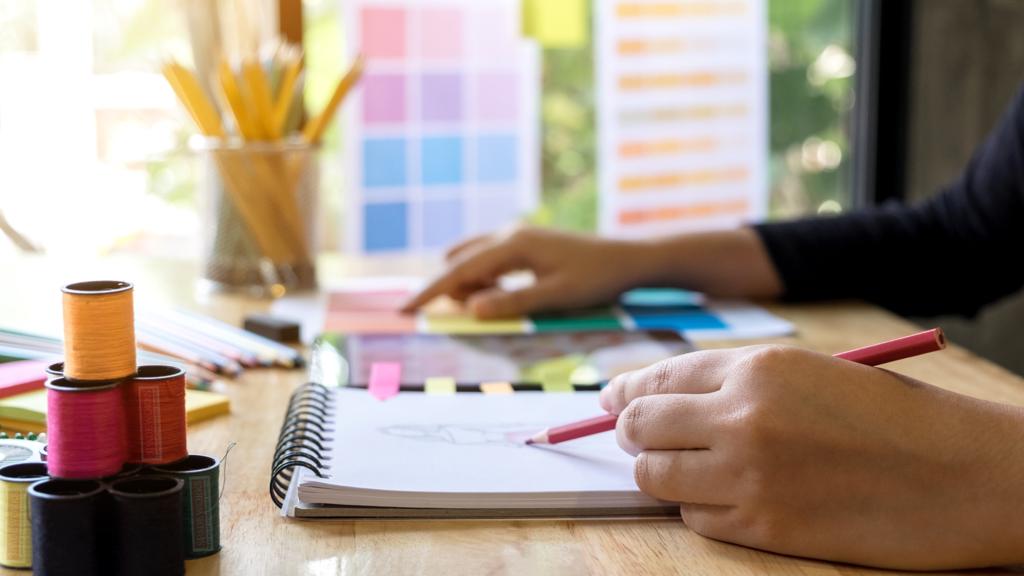
Product Development
At the start of every season we present a range of products in person to our customers. This product development is based on inspiration mood boards received from them or based on our independent research. Sustainable products, processes and accessories forms a big part of this product development.
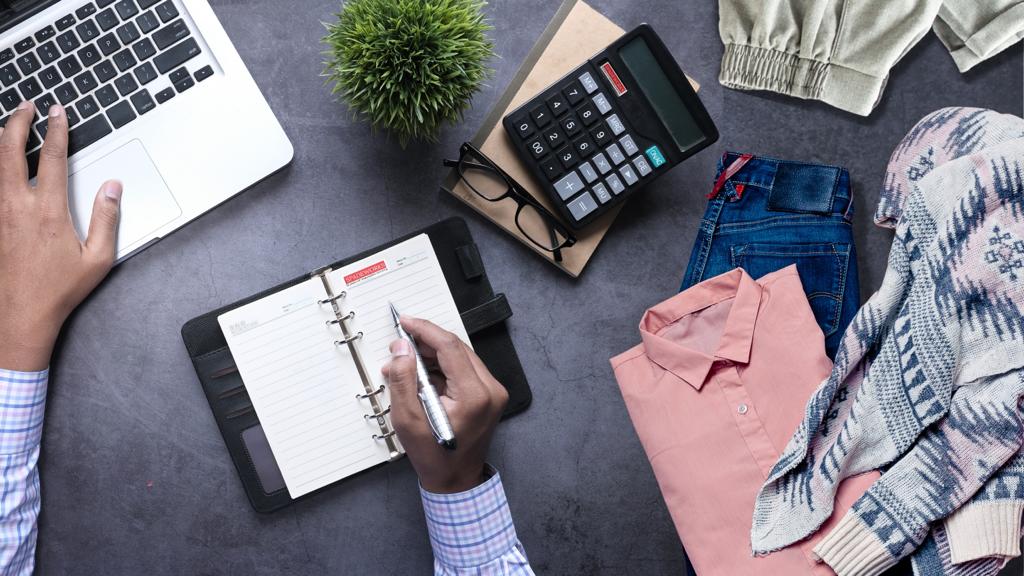
Costing
Upon selection of products from our product development presentation, a costing exercise is done to ensure selected products are within price expectations and range.
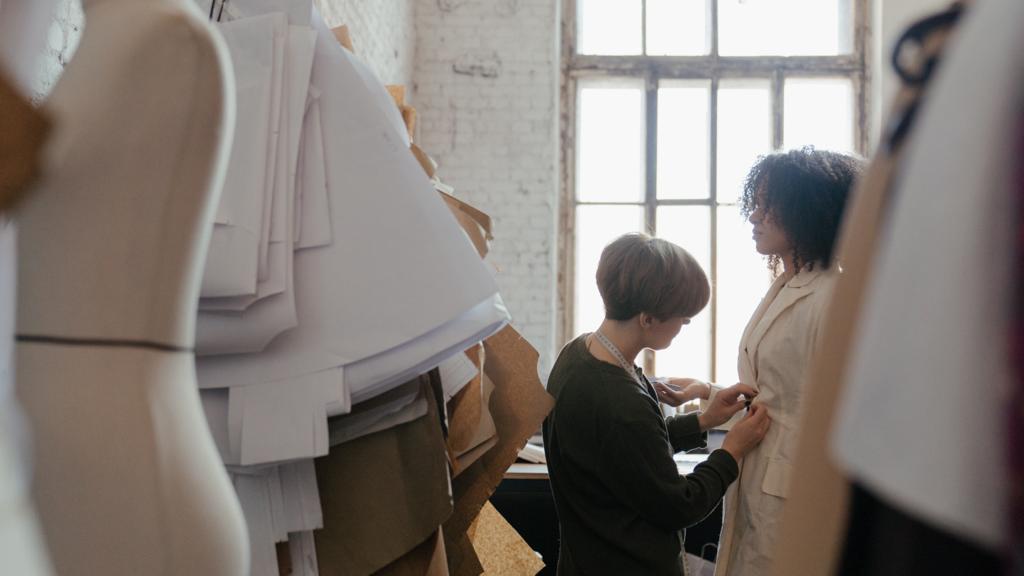
Sampling
Upon confirmation of price range, sales sample forecasts are given by our customers. Sales sampling process starts upon issuance of a sales sample PO.
For first time customers, we request an order forecast of business and signing of contract before we proceed into sales sampling.

Capacity Block
Sales samples are followed by after sales order forecast and production capacity block by customers.
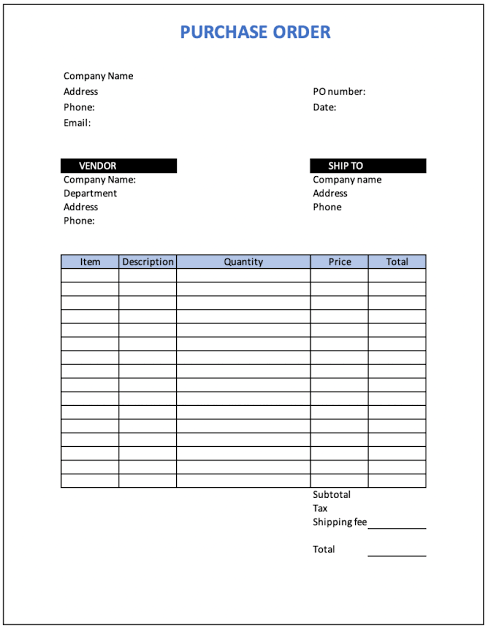
Purchase Order Release
Bulk order placement is marked by the release of a formal purchase order by the customer. The purchase order contains clear details of order quantity, confirmed price, confirmed delivery (ex-factory), shipment mode and payment mode.
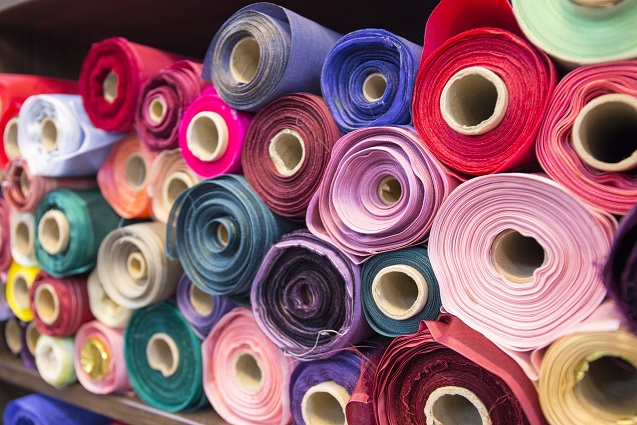
Raw Material Order
Raw material ordering is effected after receipt of a formal Purchase Order.
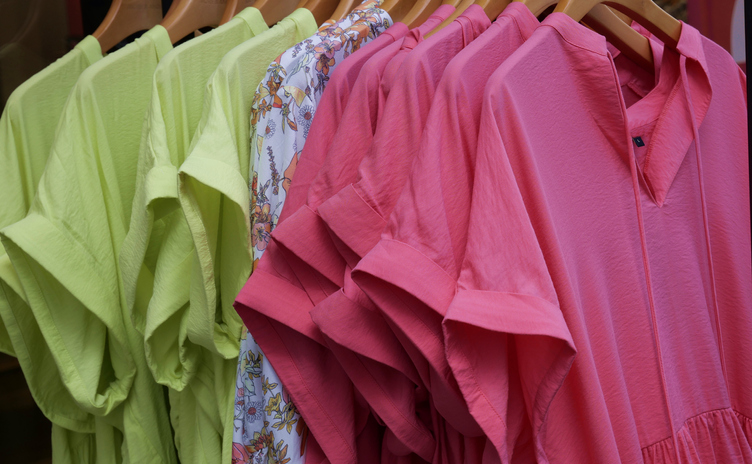
Pre-Production Sample
Upon receipt of raw materials ( fabric and accessories), a pre-production sample (one size or size set) is sent to the customer. This sample is a representation of what the final bulk production would be. Customer is expected to approve this sample for before a formal start of bulk production.

Production Size Set and Pilot Run
Upon approval of a pre-production sample and receipt of all bulk raw materials, a full size set is made at the factory for QA review and approval. On approval of the size set, a pilot run (of about 50pcs) across all size is again made for QA review and approval. The purpose of the pilot run is to simulate a mini bulk production and ensure all requirements (especially shrinkage and measurements) are in order.
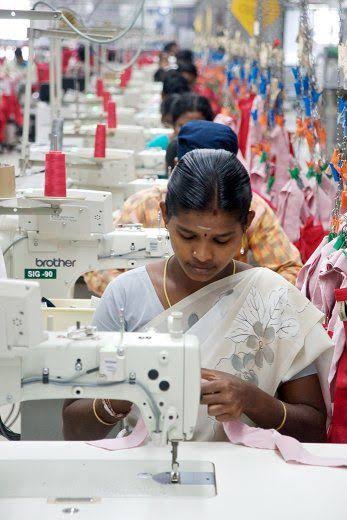
Production Start
Bulk production begins after approval of size-set and Pilot run.
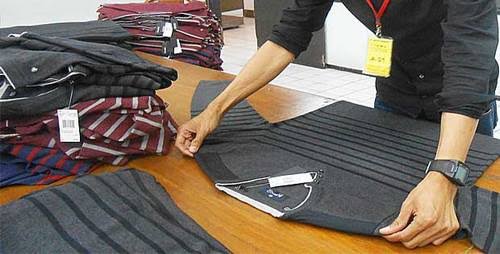
In-Line Checks
Our QA team is stationed at the factory from the beginning of bulk production till the end. In-line quality control checks are done every day during production and reports of the same are sent to the head office and customers if required.
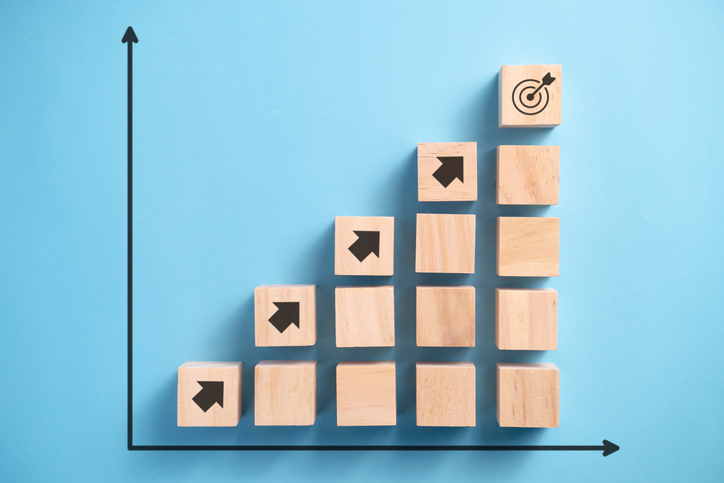
Weekly Production Updates
Production status and updates are monitored every week by merchandising and logistics team at Fresh Sourcing to ensure on-time deliveries. Issues if any that might affect a contracted delivery date are escalated to the customers as an alert and further planning.
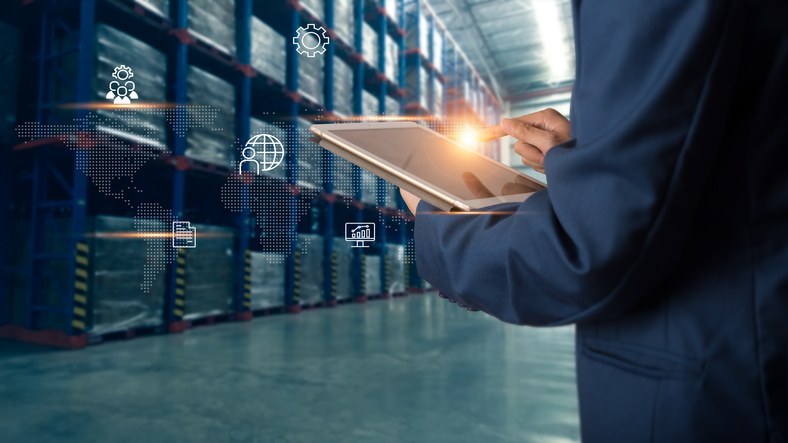
Delivery and Inspection Planning
Based on weekly production updates, delivery planning and inspection planning are done accordingly. QA team along with logistics team plan final inspections at various production facilities.
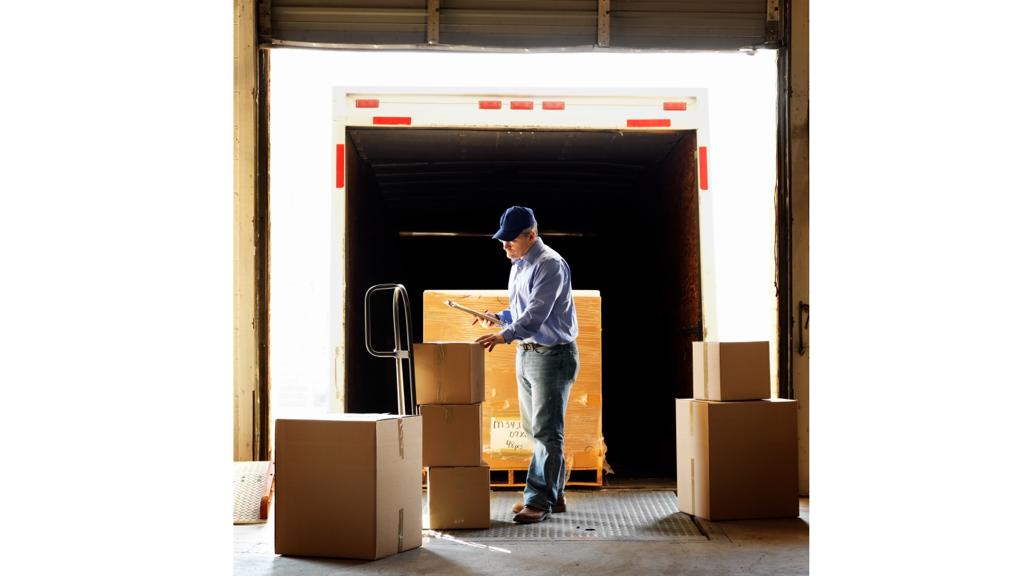
Shipment Planning and Booking to Forwarder
Based on inspection planning, Fresh Sourcing’ logistics team advises shipment planning to the customer and issues booking to the nominated forwarders for effecting shipments from the factories.
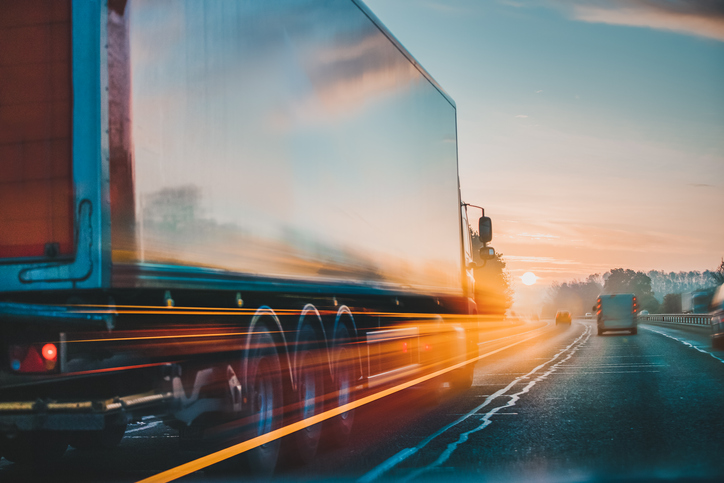
Goods Despatch
Upon handover of goods to the nominated forwarder, Fresh Sourcing’ logistics team advises customer of the same along with shipment details.
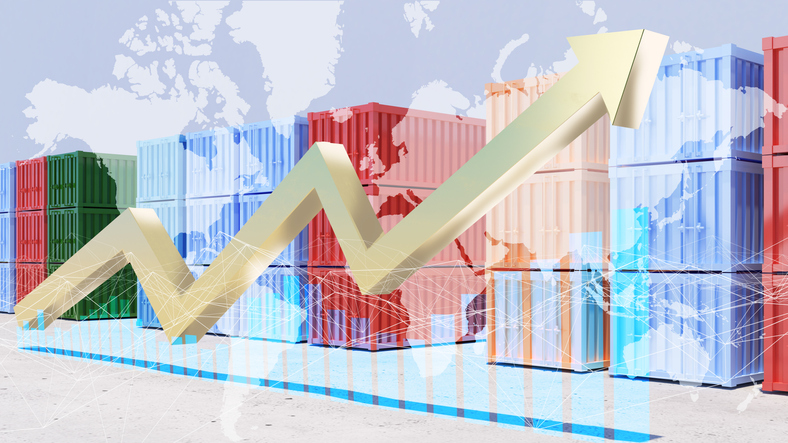
Delivery Performance
Our execution skills and process control are a key driver of our business and growth. Needless to say our delivery performance over the last 15 years has averaged a proud 95%.